工場作業の効率化とは?現場のムダを減らす改善策と成功事例を解説
工場現場で「人手が足りない」「作業が非効率だ」と感じたことはありませんか?
実は、作業のムダや属人化を放置しておくと、生産性の低下だけでなく品質トラブルにもつながります。
本記事では、工場作業を効率化するメリットや非効率の原因、すぐに実践できる改善策から、実際の成功事例までを網羅的に解説します。今日から現場で使える改善のヒントを、ぜひ見つけてください。
「現場に合った改善策が知りたい」「自社に合う効率化の支援を受けたい」とお考えの方へ。
当社では、現場に寄り添った改善支援や、作業の見える化・自動化に関するアドバイスも行っています。
まずはお気軽にお問い合わせください。
工場作業を効率化とは?
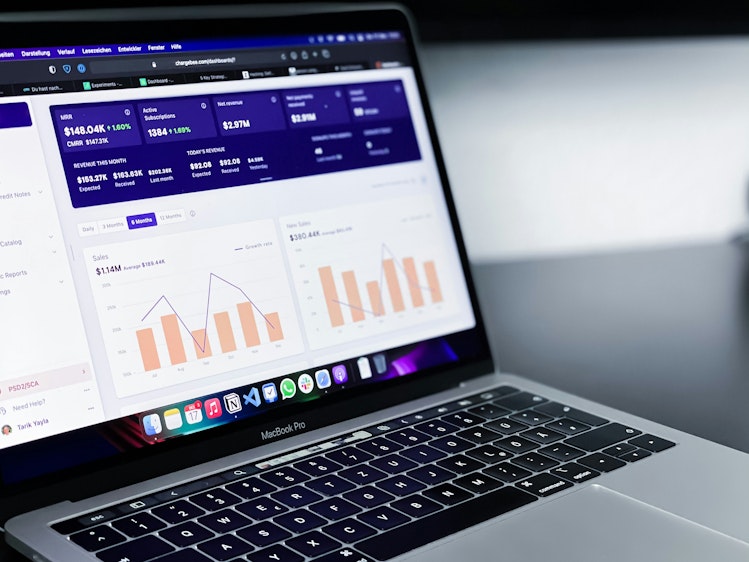
工場作業の効率化とは、作業にかかる時間や手間を減らしながら、生産性・品質・安全性を維持・向上させることを指します。単に作業スピードを上げるのではなく、工程のムダを減らし、属人性をなくし、誰がやっても安定した結果が出せる状態を目指す取り組みです。
特に近年では、人手不足や納期短縮、品質要求の高まりといった課題を背景に、工場現場の効率化が急務となっています。作業手順の標準化、レイアウト改善、5S活動、ITツールの活用など、さまざまな手法がありますが、重要なのは現場の実態に即した施策を地道に積み重ねることです。
工場全体の成果を高めるために、まずは「作業の効率化」が何を意味するのかを正しく理解し、自社の課題に合わせたアプローチを検討することが求められます。
工場作業の効率化を図る3つのメリット
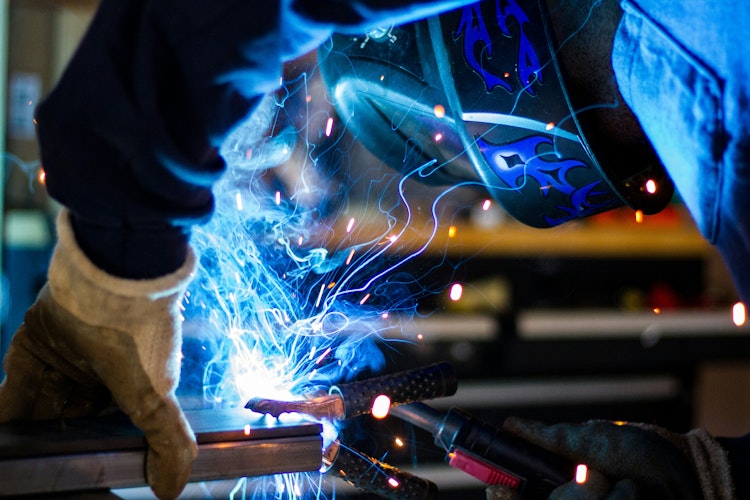
次に、工場作業の効率化によって得られる代表的なメリットを3つに整理して解説します。
- コスト削減できる
- 品質向上を図れる
- 人手不足対策ができる
工場運営の課題を解決するヒントとして、ぜひ参考にしてください。
コスト削減できる
工場作業を効率化する最大のメリットのひとつは、コストの削減です。作業の重複や無駄な移動時間、余剰在庫、作業ミスなどを見直すことで、人件費や材料費の浪費を防ぐことができます。
たとえば、レイアウト変更によって動線を短縮し、1日の作業回数を増やした事例では、月間で10%以上の作業時間短縮が実現されました。
また、印字や計測などの単純作業を自動化することで、1人あたりの処理量を大幅に増やせた企業もあります。限られた人材でより多くのアウトプットを出すためには、コスト構造の見直しが不可欠です。
品質向上を図れる
効率化は品質向上にも直結します。作業の標準化が進むことで、工程ごとのバラつきや人的ミスが減少し、不良品率の低下につながります。
たとえば、作業マニュアルやチェックリストを導入した現場では、ヒューマンエラーによるトラブルが年間で30%削減されたという報告もあります。
さらに、見える化によってリアルタイムで異常を把握できるようになると、初期対応が迅速に行え、品質の安定化が可能になります。結果的にクレームや再作業も減り、信頼性の高い製品づくりが実現できます。
人手不足対策ができる
深刻化する人手不足に対しても、効率化は有効な対策となります。現場において1人あたりの生産性を高めることで、同じ人数でもより多くの成果を出せるようになります。
例えば、作業の見直しと教育の仕組みを整備した工場では、従業員数を増やさずに生産量を15%以上向上させた事例があります。
また、作業を分かりやすく・簡単にすることは、未経験者や外国人労働者の早期戦力化にもつながります。人材不足が深刻な業界ほど、効率化による省人化の工夫が求められています。
工場で作業効率が悪くなる主な3つの原因
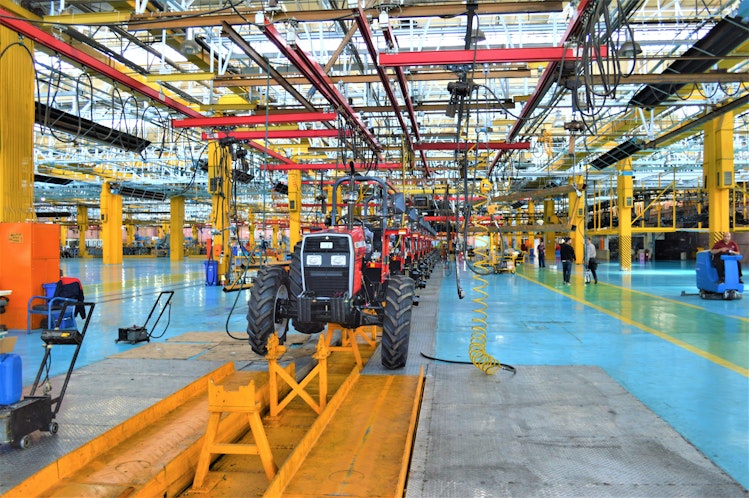
工場現場では「効率が上がらない」「人が多くても回らない」といった課題が多く見られます。これらの原因は、現場特有の構造的な問題に起因していることがほとんどです。ここでは、作業効率が低下する主な要因を3つに分けて解説します。
- 作業ミス・ムダな動線・人材の偏りがある
- 標準化・マニュアルが不足している
- コミュニケーション不足や多能工化の遅れが発生する
改善の第一歩として、現場に潜む非効率の正体を把握しましょう。
作業ミス・ムダな動線・人材の偏りがある
作業効率が悪化する原因のひとつに、作業工程における「ムリ・ムダ・ムラ」が挙げられます。たとえば、部材や工具の配置が悪く、必要なものを取りに行くたびに作業者が往復している場合、1日あたりの移動時間が30分以上発生することもあります。
さらに、同じ作業でも熟練者と初心者で品質やスピードに大きな差が出るケースも多く、特定の作業者に負荷が集中してしまう「人材の偏り」も大きな問題です。このようなロスは現場で可視化しづらいため、意識的な観察と改善が求められます。
標準化・マニュアルが不足している
作業内容が標準化されておらず、マニュアルも整備されていない場合、作業者によって手順がばらばらになり、時間と品質の両面でムダが生まれます。特に属人的な作業が多い職場では、教育コストが高く、新人が戦力化するまでに時間がかかる傾向があります。
現場でのヒアリングを通じて、実際の作業手順を見える化し、それをベースにマニュアルを作成することで、作業の均質化とミスの削減が可能になります。標準化は効率化の土台であり、改善活動の第一歩といえるでしょう。
コミュニケーション不足や多能工化の遅れが発生する
工場現場では、担当作業が固定化されすぎていることにより、作業者の間で業務の共有が進まないケースが多くあります。急な欠勤やライン変更などに柔軟に対応できず、生産ライン全体がストップするリスクもあります。
また、業務改善のアイデアや課題が現場から吸い上げられない場合、潜在的な非効率が長期間放置されてしまいます。多能工化と現場での情報共有が進むことで、作業の属人化を防ぎ、チーム全体の生産性向上が図れます。
工場作業効率化の具体策5選
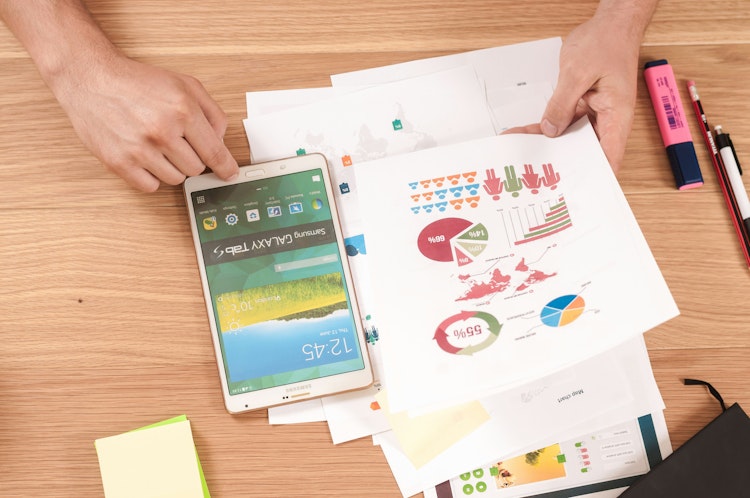
工場現場での効率化には、日々の作業に直結する「小さな改善」を積み重ねることが鍵です。作業者の動線や工程の見直し、ツールの整備など、今すぐ取り組める施策からスタートするのが効果的です。ここでは、多くの現場で実践されている代表的な効率化手法を5つご紹介します。
- 作業手順の標準化とマニュアル整備
- 設備レイアウトの最適化
- 備品・工具の5Sと整頓改善
- 作業工程の見直しと時間短縮
- 現場の声を活かした小さな改善の積み重ね
それぞれの施策について、具体的な効果や実践例をもとに解説します。
作業手順の標準化とマニュアル整備
作業を標準化することで、誰が担当しても同じ品質・スピードで仕事を進められるようになります。これにより、新人教育の時間が短縮され、作業の属人化による品質ばらつきも防げます。
たとえば、ある部品製造工場では、動画と写真を使ったマニュアルを導入したことで、新人が独力で作業できるまでの期間を約2週間から5日に短縮しました。標準化された手順は、改善提案や作業分析のベースにもなり、持続的な効率化を支えます。
設備レイアウトの最適化
設備や作業台の配置が非効率だと、移動や作業準備に無駄な時間がかかります。レイアウトを見直すことで、作業者の動線を短縮し、滞在時間を最適化することが可能です。
たとえば、1日のうち作業者が道具を取りに行く回数を減らすだけで、年間数十時間のロス削減につながる場合もあります。改善の第一歩として、作業現場を動画で記録し、無駄な移動や姿勢の変化を可視化する方法も効果的です。
備品・工具の5Sと整頓改善
工場の基本である5S(整理・整頓・清掃・清潔・しつけ)は、作業効率化にも直結します。たとえば、「どこに何があるか分からない」「同じ部品が二重に保管されている」といった状態は、探す時間のロスやミスの原因になります。
工具や部品の置き場所を定め、定期的に見直すことで、作業効率を安定的に高めることができます。また、視覚的に管理された整頓された現場は、安全性や品質にも良い影響を与えます。
作業工程の見直しと時間短縮
作業工程の中に不要なステップや順番の入れ替えが可能な箇所がある場合、それらを見直すことで大幅な時間短縮が可能です。たとえば、組立工程において部品供給のタイミングを変えることで、1工程あたり15秒短縮できた例もあります。
タイムスタディ(時間分析)や作業サイクルの計測を行うことで、改善点が明確になり、短時間で実行可能な改善を見つける手助けになります。
現場の声を活かした小さな改善の積み重ね
効率化のヒントは、現場作業者の日常に多く隠れています。「ここがやりづらい」「もっと簡単にできる方法がある」など、現場の声を拾い上げることで、実用的な改善案が生まれます。
たとえば、作業者が自主的に工夫した治具や専用ツールが、全体の作業スピードを10%以上向上させた事例もあります。現場参加型の改善活動を推進することで、自律的な改善文化を根付かせることができます。
成功事例から学ぶ!現場改善のアイデア集
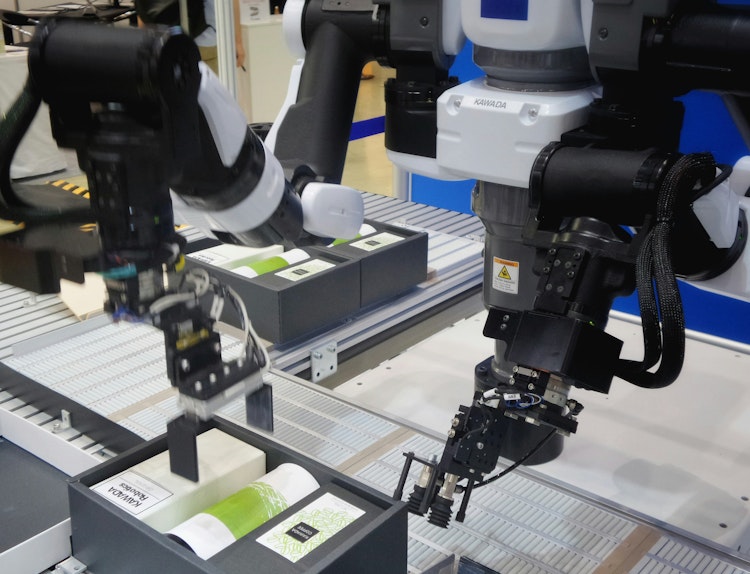
実際の工場現場では、工夫次第で大きな効率化を実現しているケースが多くあります。「どのように改善を進めたか」「どんな効果があったか」を知ることは、自社の改善活動のヒントになります。ここでは、特に成果が出た代表的な現場改善の事例を3つ紹介します。
- 印字自動化による作業時間の短縮
- 見える化によるミス削減
- 省人化の工夫
手間をかけすぎず、現場の負担も少ない取り組みばかりです。ぜひ参考にしてみてください。
印字自動化による作業時間の短縮(スタンプ活用)
製品や梱包資材への印字作業は、単純ながら時間と手間がかかる工程です。ある食品工場では、作業者が手書きで日付やロット番号を記入していたため、1日数百回の書き作業が発生していました。
そこで、専用スタンプと自動印字装置を導入した結果、1回の印字が2秒以内で完了するようになり、1日あたり約2時間の作業時間削減に成功しました。また、手書きによる表記ミスもゼロになり、品質管理の観点でもメリットが得られました。
見える化によるミス削減(IoTセンサーの事例)
作業ミスや工程の遅れは、発生した時点で把握できないと重大なロスにつながります。ある金属加工工場では、IoTセンサーを使って機械稼働の状況や温度変化、エラー履歴をリアルタイムで可視化する仕組みを構築しました。
これにより、異常を即座に検知して対応できるようになり、月あたりのトラブル発生件数が25%減少。また、稼働率が数値で明確になったことで、改善の優先順位をつけやすくなり、作業の最適化も進みました。
省人化の工夫(ロボット・AGV活用)
人手不足に対応するために、省人化の取り組みは欠かせません。ある中小製造業では、部品運搬に無人搬送車(AGV)を導入。
以前は作業者が1日中カートで資材を移動していましたが、AGVに任せたことで作業者の移動距離を80%以上削減。空いた時間を生産作業に充てられるようになり、1人あたりの生産性が20%以上向上しました。また、安全面でもぶつかりや転倒リスクが減り、現場の負担軽減にもつながりました。
導入前に押さえておくべきポイントと注意点
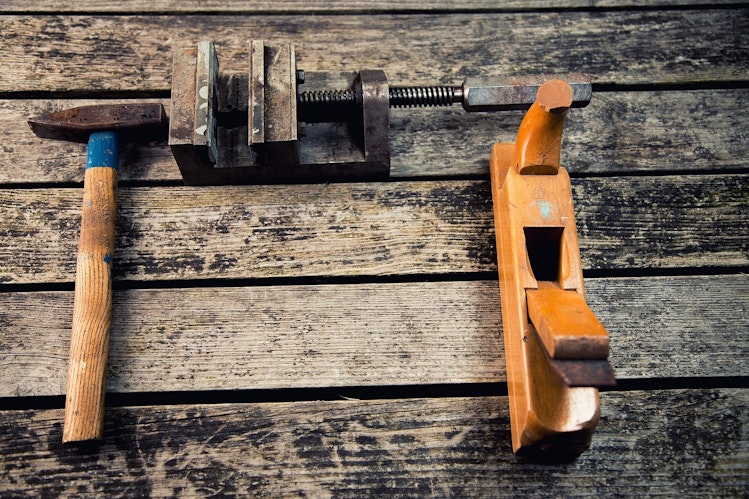
工場作業の効率化に取り組む際は、単に改善策を導入するだけでなく、「どのように進めるか」が成功のカギになります。拙速な導入や現場の負担増につながる進め方を避け、段階的・持続的に取り組む姿勢が重要です。以下に、導入時に意識すべき代表的な注意点を紹介します。
- まずはスモールスタートで進める
- 改善後の負荷・現場負担を確認する
- 技術・技能の継承と属人性の回避策を考える
長期的に成果を出すための土台として、ぜひ確認しておきましょう。
まずはスモールスタートで進める
効率化の施策は、一度に全体へ適用するのではなく、まずは特定の工程やエリアに限定して実施するのが効果的です。たとえば、作業手順の標準化をライン全体で始めようとすると、調整項目が多くなり、現場に混乱を招くリスクがあります。
そこで、改善効果が見えやすい工程からスモールスタートを行い、現場での成功体験を積むことで、他部署への展開がスムーズになります。また、失敗した場合のリスクも最小限に抑えられます。
改善後の負荷・現場負担を確認する
効率化を進めるなかで、作業者に過剰な負担がかかるような仕組みになると、逆にモチベーション低下や離職のリスクを招く可能性があります。たとえば、チェック項目を増やしすぎたことで作業が煩雑になった事例や、省人化により1人当たりの作業量が倍増してしまったケースも存在します。
効率化は「働きやすさ」とセットで設計すべきであり、改善施策の実施後も現場の声を継続的に拾う姿勢が求められます。
技術・技能の継承と属人性の回避策を考える
作業の効率化と並行して、人材育成やノウハウの継承も意識する必要があります。特に熟練者に依存した工程が多い現場では、属人化がボトルネックとなり、新人が定着しづらいという問題が起こりやすいです。たとえば、暗黙知を形式知に変えるために動画マニュアルやOJT記録を活用する事例も増えています。
改善と同時に教育の仕組みを整えることで、組織としての生産性を底上げできます。
まとめ|工場作業の効率化は小さな改善から始まる
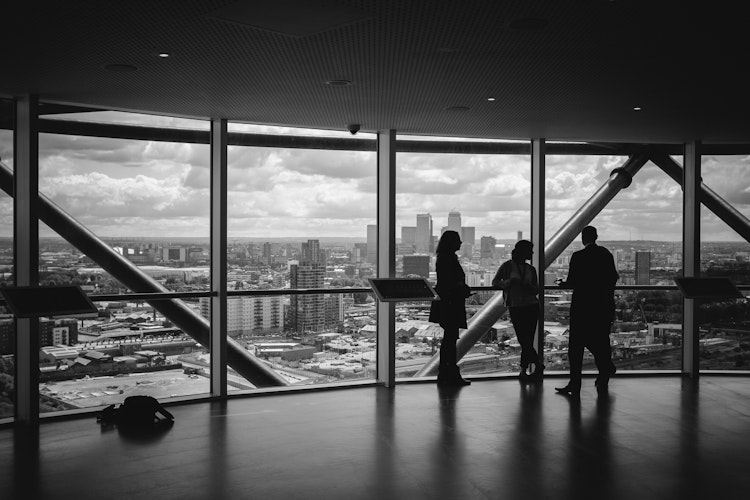
工場作業の効率化とは、単にスピードを上げることではなく、現場に潜むムダやバラつきを見直し、誰もが無理なく安定して作業できる仕組みをつくることです。コスト削減や品質向上、人手不足の解消といった大きな成果は、日々の小さな改善の積み重ねによってこそ実現します。
現場の作業ミスや非効率な動線、属人化など、改善すべきポイントは至るところにあります。作業標準化や5Sの徹底、設備レイアウトの最適化といった基本施策に加え、IoTや自動化などの事例から学ぶことで、自社に合った改善策が見えてくるはずです。
まずは、特定の工程や作業にスモールスタートで取り組み、現場の声を反映しながら改善のサイクルを回していきましょう。効率化は一過性のプロジェクトではなく、現場の文化として根づかせていくものです。今日の一歩が、明日の大きな変化につながります。
「現場に合った改善策が知りたい」「自社に合う効率化の支援を受けたい」とお考えの方へ。
当社では、現場に寄り添った改善支援や、作業の見える化・自動化に関するアドバイスも行っています。
まずはお気軽にお問い合わせください。